Rilsan Plastic Coating
At Arboles UK we use Rilsan powder coating on our laboratory taps and our emergency showers and eyewashes. This provides longevity of paint work quality, scuff resistant properties and the all important chemical exposure resistance. There isn’t any peeling, there isn’t staining, all you have is a tough hardwearing product that is made to last.
Plastic Coating
The anti-corrosive plastic coating is made of 11 polymiade in high visibility yellow, with technical features including:
- Approx. 250 to 300 microns thick.
- 184 to 186º C high melt point.
- Self-extinguishable low flammability.
- Shore hardness D to 20º C, 75.
Overall, the coating is considerably resistant against bases, sea water and saline environments: against oils, grease and aromatic solvents: to organic acids, diluted mineral acids and aliphatic solvents. Neither fungi nor micro-organisms stick to the parts, nor does frost collect on its surface.
Prepared metal parts are heated to between 300º to 450º C, prior to coating.
Resistance To Boiling Water
Excellent adhesion after 2000 hours
Resistance To Sea Water
There is no corrosion after 10 years of exposure
Resistance To Salt Spray
There is no corrosion after 2000 hours of exposure (ASTM B-117 or AFNOR X 41-002 standard)
Powder Coating and Application Method
The prepared metallic tap components are heated in an oven at a constant temperature ranging between 300°c and 450°c depending on the part mass and the nature of the metal. As soon as the part is removed from the oven it is placed for up to five seconds in the powder container. When the powder comes into contact with the hot metallic surface it melts and coats the said metallic part evenly. The part is removed from the powder container and air cooled which produces a smooth robust polished finish.
The Arboles UK guide to chemical resistance is charted below:
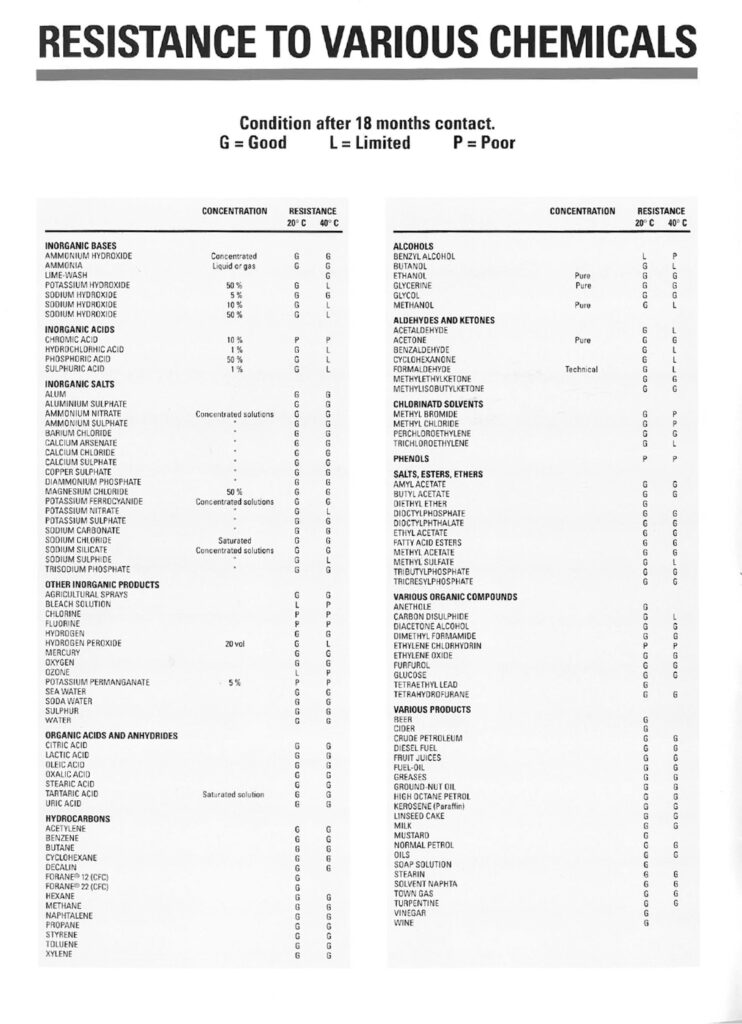